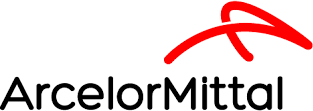
Product Quality Coordinator - Manufacturing Technology
ArcelorMittal
- Hamilton, ON
- Permanent
- Full-time
- Identify, lead, and manage quality improvement efforts and conduct quantitative analysis of quality program effectiveness
- Lead and participate in the troubleshooting and resolution of process quality problems.
- Evaluate process and product failures and consequences using formal Root Cause Analysis (IRCCA) and develop appropriate corrective actions, controls and training to eliminate/mitigate failures.
- Participate in cross-functional teams to assure product and process quality as issues arise
- Analyze process and product performance and make recommendations for improvement to leadership.
- Develop, plan and execute improvement projects as part of the annual business planning process.
- Assist to define and communicate the acceptable product release limits to customer service team and operations.
- Assist development of the internal requirements and standards to ensure customer requirements are achieved.
- Ensure that non-conforming material identified by the customer is effectively contained both internally and externally.
- Support the Product Design and Product Standards process lead by MQCI and act as liaison between the Business Unit and Metallurgy department.
- Remain fluent and up to date on new developments in processes, product, equipment and technologies for the manufacturing and processing of Steel.
- Participate in the development of risk mitigation tools such as FMEA and Control Plans in compliance with the IATF 16949 requirements
- Create and perform layered process audits to ensure compliance to the existing processes and to identify continuous improvement opportunities
- 4-year University Degree or 3-year Engineering Technologist College Diploma.
- Experience in manufacturing or a steel-related industry
- General manufacturing, maintenance and/or equipment knowledge and experience
- Understanding of metallurgy and metallurgical defect classification
- Experience with Process/Product Control and Quality Assurance systems and methods.
- Understanding of World Class Manufacturing (WCM) or World Class Continuous Improvement activities (Lean Manufacturing)
- Working knowledge of formal Root Cause Analysis (RCA)
- Knowledge in statistical analysis techniques and statistical software tools (Minitab, R, Excel)
- Understand process (mechanical, chemical) failure mechanisms and modes
- Mechanical aptitude and a “hands-on” approach to problem solving
- Knowledge of Quality Assurance concepts and methodologies
- Strong strategic thinking skills with the ability to link manufacturing processes and desired product standards
- Able to develop data queries to extract customer, product, and process data for analysis
- Strong problem-solving, analytical and troubleshooting skills
- Strong interpersonal skills with the ability to build strong relationships with a diverse workforce
- Ability to influence and lead others
- Required to work in both a manufacturing and plant office environment
- The manufacturing plant environment includes exposure to dust, chemicals, temperature changes, noise, and large industrial equipment.
- Required to travel to Customer plants or Outside Processors. Able to accommodate cross-border travel (up to 2-3 days at a time)
- We provide employees with a market competitive total compensation package. Our promise is to provide superior pay for superior performance, accompanied by comprehensive health and wellness, pension, vacation and related programs.
- Competitive hourly rates and shift premium
- On your first day you will immediately be eligible for:
- Bonus paid quarterly based on Company performance on key goals. Your bonus target will be 10% of base salary earnings.
- Company paid Defined Contribution Pension Plan. No employee contribution required. With employer contributions between 5 and 10%.
- Competitive vacation allowances
- Group Benefits with no health and dental premiums.
- For health and dental claims you only pay amounts above the maximums the plan pays.
- Life insurance premiums are shared with the company.
- Competitive vacation entitlements
- PPE and workwear provided at no cost (if required)
- Wellness and Employee Assistance Programs
- Free access to three onsite fitness centers and our 70-acre recreation park with multiple arenas, fields and organized sports for you and your family